Rubber Compression Molding
What is rubber compression molding?
Rubber compression molding forms uncured rubber into a desired shape. First, the elastomer is pre-heated until pliable and then put into an open mold cavity. Closing the mold forces the rubber to fill the cavity, where the elastomer is keep under heat and pressure until cured.
The advantages of rubber compression molding include:
- Lower tooling costs
- Small production runs
- Suitable for larger, heavier parts
Rubber Compression Molding Steps:
- Uncured rubber is preformed to control weight, shape and specification
- Rubber preform is placed into the mold cavity.
- Rubber mold is closed compressing the rubber to fill the mold's cavities
- Mold remains closed under pressure and temperature to reach optimal cure
- Compressed rubber parts are removed from the mold and the process is ready to begin again
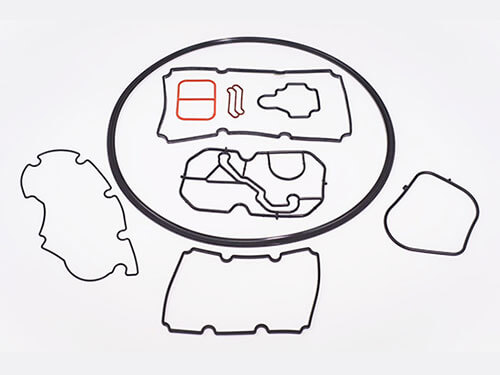
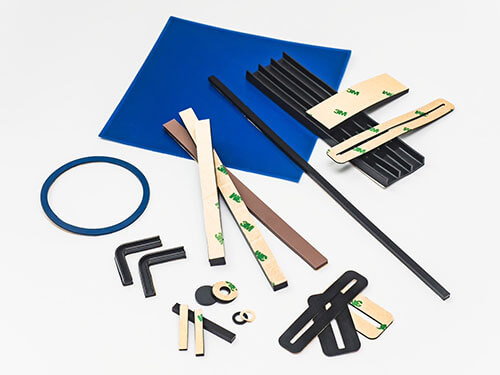
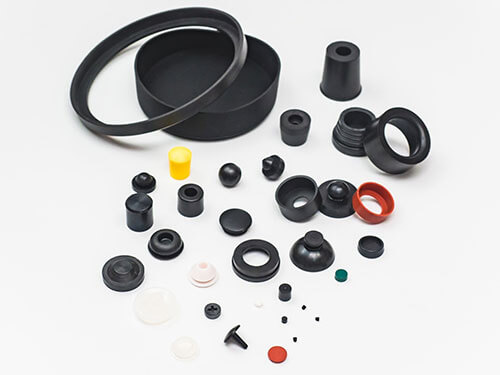
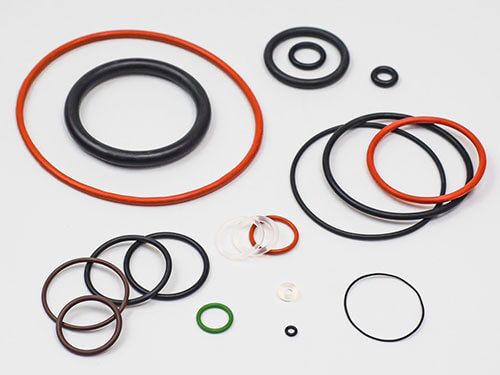

Rubber Compression Molding Tools:
Rubber compression molding tools are essential for shaping and forming rubber materials into desired products. These tools are designed to withstand high pressure and temperature, ensuring that the rubber fills the mold cavity completely and cures properly. The primary components of rubber compression molding tools include:
- Mold Cavity: The hollow part of the mold where the rubber material is placed and shaped.
- Platen: The flat plates that apply pressure to the mold, ensuring the rubber fills the cavity uniformly.
- Heating Elements: Integrated heating systems to maintain the required temperature for curing the rubber.
Using high-quality rubber compression molding tools ensures precision, efficiency, and durability in the production process. The reliability and accuracy of these tools directly impact the quality of the final rubber products, making them an essential investment for manufacturers aiming for excellence in rubber molding.
-
compression molding&tool
-
compression molding&tool