Rubber Injection Molding
Basic Intro of Rubber Injection Molding
Rubber injection molding feeds uncured rubber from a hopper into heated barrel. A screw-type plunger then pushes the elastomer into a heated chamber. This material flows through a gate and runner system into mold cavity. The mold remains at the proper temperature until the rubber is cured.
The advantages of rubber injection molding include:
- Quicker cycle times
- Custom shapes with little flash
- Support for wide range of durometers
Rubber Injection Molding Steps:
- Material in injection unit ready for injection into cavity
- Material is injected from injection unit through runner system & gates into cavities.
- Parts (material) are cured in mold until the cure process is completed.
- Molded rubber parts are removed from mold and the process is ready to begin again.
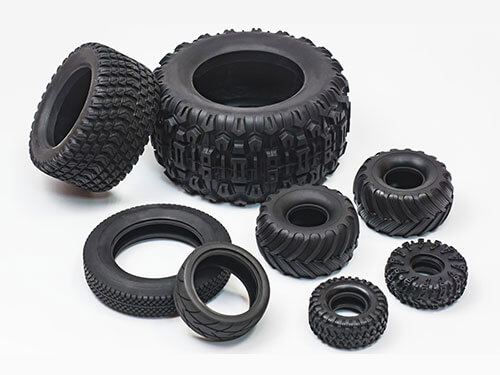
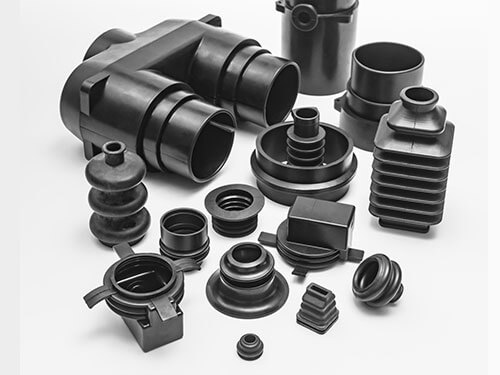
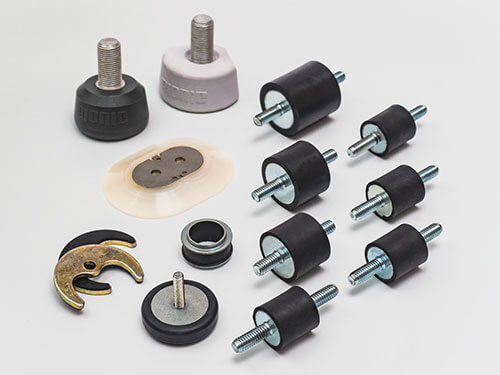
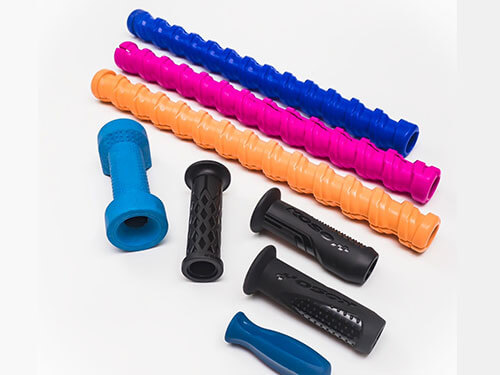
Rubber Injection Molding Tools:
Rubber injection molding tools are essential for creating high-quality rubber parts with precision and efficiency. These tools include molds, injection units, and other specialized equipment designed to handle the unique properties of rubber materials.
Advantages of using high-quality rubber injection molding tools includes:
- Enhanced precision and consistency in the final product
- Reduced cycle times and increased production efficiency
- Minimized material waste and lower production costs
- Improved durability and lifespan of the molds and other tools
Rubber injection molding is a highly efficient and precise method for producing custom rubber parts. By using the right tools and following the proper steps, manufacturers can achieve superior quality, reduced waste, and increased production efficiency. Contact us today!
-
Injection Molding & Tool
-
Rubber Injection Molding