- HOME
- Industries Served
- Medical
Silicone Rubber for Medical Device Applications
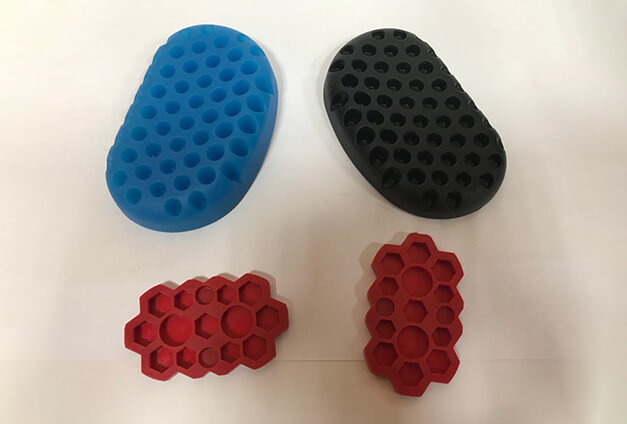
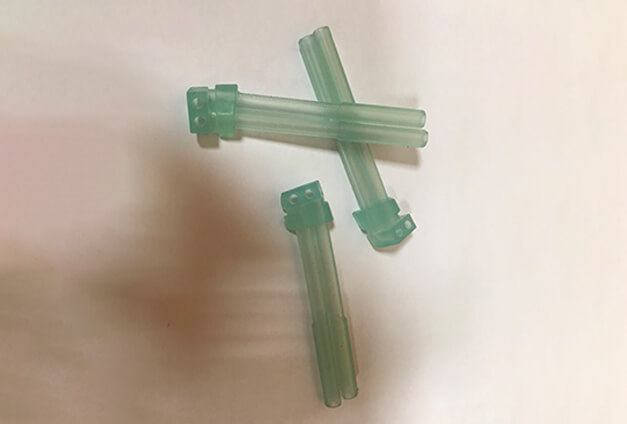
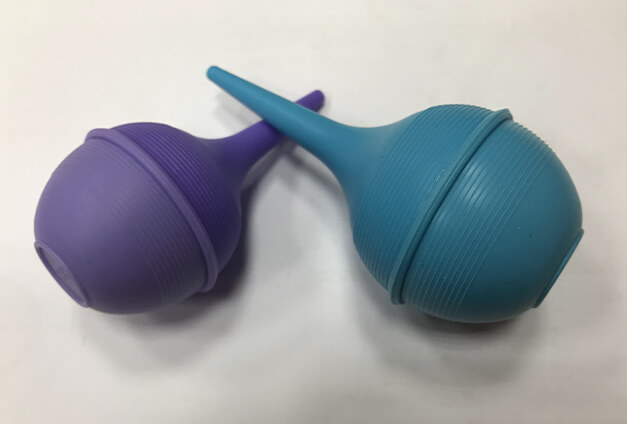
Rubber Parts for Medical & Healthcare Industries
The highly adaptable characteristics and durability of rubber make it an ideal material for the production of a vast array of medical items. Rubber is used in the medical industry for the production of seals, gaskets, and tubing used in medical equipment; rubber diaphragms; rubber insulation for cords; rubber gloves; and other medical equipment and parts.
Advantages of Rubber Medical Parts
There are several advantages of using rubber in the medical industry:
1. Sanitation and Biocompatibility
The rubber used in medical equipment applications must be of high quality to remain sanitary when making contact with patients. Because medical equipment often comes in contact with body fluids, the rubber used for these applications must be biocompatible and chemically stable. It also must be durable enough to resist degradation when exposed to high temperatures during sanitation. Rubber is heat- and chemical-resistant, which makes it easy to sterilize using methods such as steam sterilization, autoclaving, or chemical sterilization.
2. Flexibility
Rubber is versatile and can be formed into a variety of shapes, so it is useful in making medical products such as tubing, gloves, and seals.
3. Affordability
Rubber is an inexpensive material for production and processing, making it an ideal choice for medical applications.
4. Low friction
Rubber has low friction which makes it useful for applications that require sliding, like catheters and syringe plungers.
Industry Regulations and Requirements
Due to the extreme importance of quality control for medical products, rubber products used in medical applications must strictly adhere to regulations and guidelines set by governments for the protection of the public. All products must be produced in safe, contamination-free production facilities, with production procedures and certification overseen and regulated by government or third-party agencies such as the FDA, NSF, UL, CE, etc.
Jhao Yang Quality
In 1980, Jhao Yang started manufacturing silicone rubber healthcare products and orthopedic equipment components. We apply industry-leading manufacturing processes, rubber formulations, and quality controls to produce many FDA, NSF, UL, CE, BSCI, WRAS, and KTW-certified products. We have our own mold department that does in-house tooling to ensure high-quality, medical-grade rubber parts. We are capable of handling complex designs and extensive customer requirements and welcome you to contact us for any of your medical equipment rubber needs.