Rubber Molding: A Versatile Manufacturing Process
Rubber molding is a production technique that involves injecting rubber material into a mold cavity to create rubber products. The rubber is then solidified by heating or cooling the mold. This method is widely employed in the manufacturing of automotive parts, appliances, and medical devices.
Rubber Molding Process
The typical procedure for rubber molding encompasses the subsequent stages:
- Preparation of materials: Rubber materials are mixed with a range of additives, including vulcanizing agents, fillers, and colorants.
- Molding: The prepared rubber material is injected into the mold cavity and subjected to either heating or cooling to achieve solidification.
- Demolding: Once the rubber has undergone the curing process, the product is extracted from the mold.
- Finishing: The products undergo trimming, inspection, and packaging as part of the finalization process.
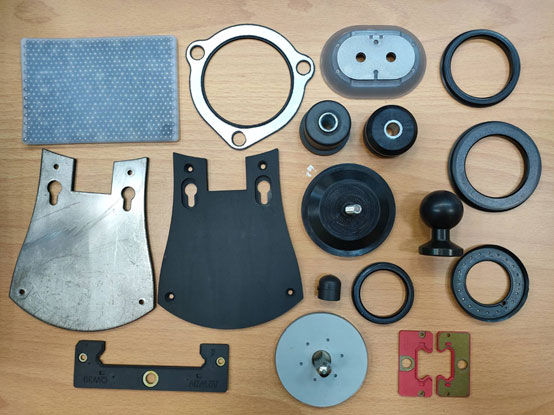
Advantages of Rubber Molding
Rubber molding presents numerous advantages over alternative manufacturing processes. One notable advantage is its versatility, as it enables the production of products in various shapes and sizes. Additionally, rubber molding allows for material flexibility by utilizing different types of rubber, each possessing its distinct properties. Moreover, this manufacturing process is cost-effective, making it a practical choice. Lastly, rubber molding ensures high productivity by facilitating the rapid production of large quantities of products.
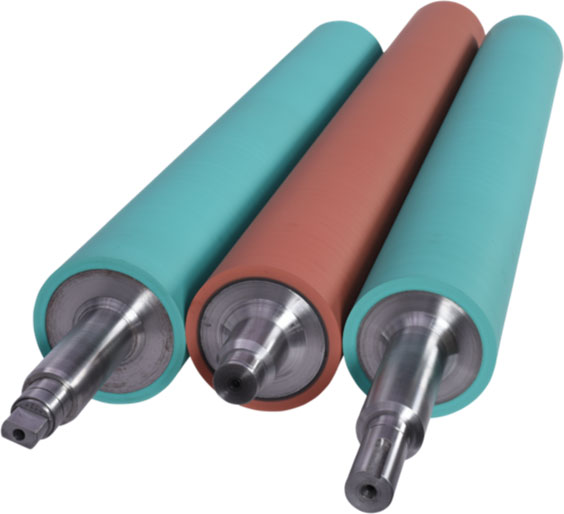
Which Industries Are Rubber Molding Used In?
Rubber molding is used in a variety of industries, including:
- Automotive: Rubber molding is commonly used in the automotive industry to manufacture parts such as tires, seals, gaskets, hoses, and belts. These applications benefit from rubber's durability, flexibility, and resistance to wear and tear.
- Electrical: Rubber molding plays a crucial role in creating electrical insulation, seals, and gaskets for equipment like power lines, transformers, and motors. Rubber's excellent electrical insulation properties and resistance to high temperatures and chemicals make it an ideal material for these applications.
- Aerospace: Within the aerospace industry, rubber molding is a vital process used to fabricate seals, gaskets, hoses, and connectors for both aircraft and spacecraft. The utilization of rubber in these applications is particularly advantageous due to its lightweight composition, long-lasting nature, and exceptional resistance to extreme temperatures, pressure, and vibration.
- Home appliances: Rubber molding is used to make seals, gaskets, hoses, and electrical insulation in appliances such as refrigerators, washers, and dryers. Rubber is an ideal material for these applications because it is durable, flexible, and resistant to high temperatures and chemicals.
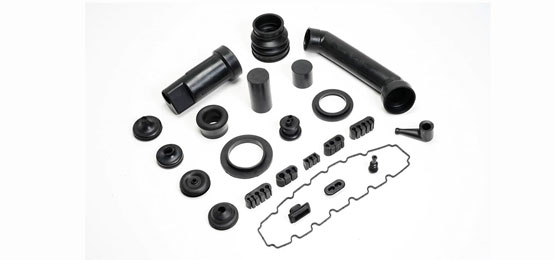
Other Applications for Rubber Molding
Rubber molding is also used in a variety of other industries, including:
- Agriculture: The needs of the agriculture industry may seem different compared to other manufacturing sectors. In agriculture, it is essential to have protection against leaks and seepage, while also being able to endure the challenging weather conditions that all agricultural products must face. Chemical fertilizers and bug repellents play a crucial role in agricultural production, and their careful handling is of utmost importance. Rubber molding plays a significant role in manufacturing gaskets and seals that offer the necessary protection and safety required for handling the various chemicals used in agricultural production.
- Medicine: Rubber molded products play a crucial role in the medical field, serving various purposes such as sealing equipment, providing fluid through tubing, and more. The inherent qualities of rubber, including its durability, make it an ideal material for medical applications. Whether it is in medical research or patient treatment, rubber-molded parts and products are extensively utilized. One of the key advantages of these products is their recyclability, which is particularly important in medical settings where instruments are often used once and then disposed of. Additionally, manufacturers prioritize meeting the stringent standards and regulations in place to ensure the safety and well-being of patients.
- Food and Beverage: Standards for rubber-molded products for the food and beverage industry must comply with regulations set by the federal government's Food and Drug Administration (FDA). Products must be designed to meet special hygienic conditions and be able to withstand regular cleaning and disinfection. The FDA regulates acceptable types of rubber compounds that can be used to produce parts used in the food and beverage industry. The main concern is that the material is non-toxic and non-carcinogenic.
- Print: In the printing industry, molded rubber products find significant applications in the form of rubber rollers. These rollers, comprising a metal core, rubber bonding material, and a rubber covering, are indispensable for the smooth transfer of ink onto printing plates. Moreover, rubber pads and mountings are widely employed to absorb shocks, thereby improving the efficiency and longevity of printing machinery.
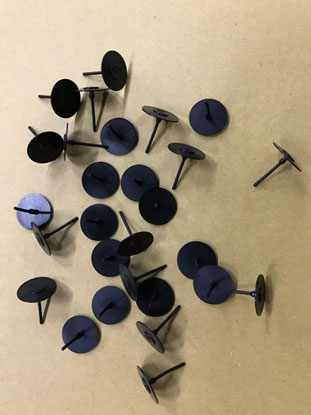
In conclusion, rubber molding has a wide range of applications across various industries. Its durability, flexibility, and ability to withstand extreme conditions make it a valuable component in the production processes of aerospace, automotive, electrical, home appliances, and other industries. The versatility of rubber-molded products makes them an essential part of modern manufacturing and production, ensuring the safety and efficiency of various industrial processes.
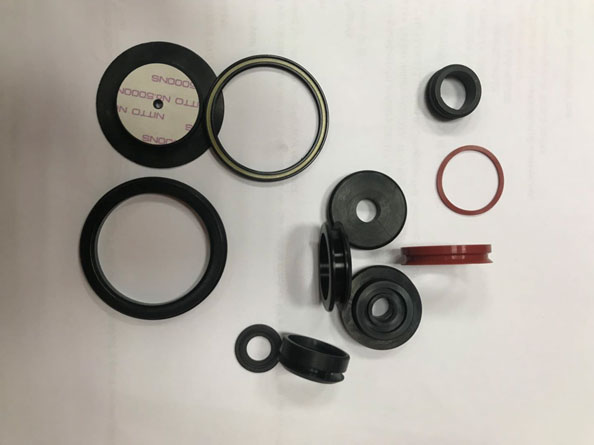